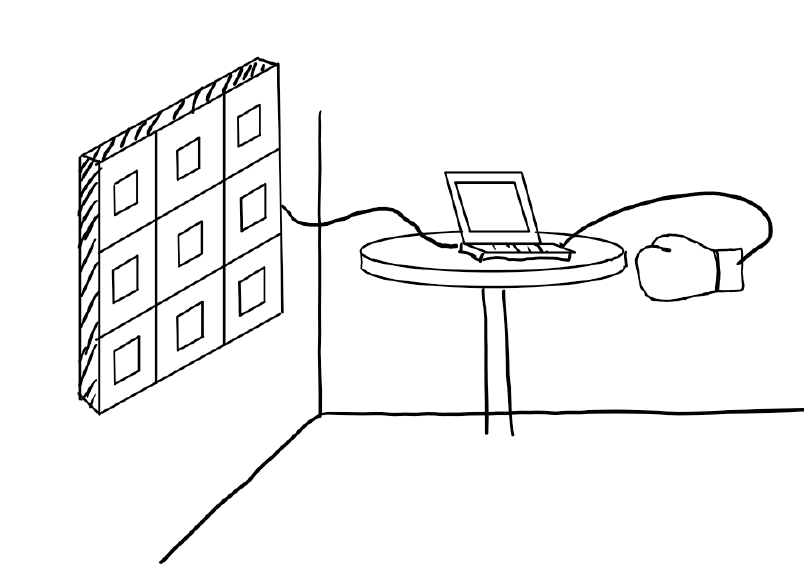
Strike Board
Boxing Rehabilitation Tool
Boxing Rehabilitation Tool (Strike Board)

The Boxing Rehabilitation Tool, or the Strike Board, was developed during my MECH 2502: Instrumentation and Measurement Techniques course at York University. This project aimed to address the challenges faced by injured boxers and patients undergoing arm mobility rehabilitation. These individuals often struggle with tracking their progress and maintaining proper movement form, which can delay recovery.
The Strike Board integrates resistive force sensors and accelerometers to measure punch force, accuracy, speed, and wrist rotation. Real-time data is processed and displayed using LabVIEW, enabling users to receive immediate feedback on their performance.
​
My specific role involved designing and assembling the prototype, integrating the sensors into the board, and calibrating the system for optimal data accuracy, i effectively contributed to programming the LabVIEW interface to process and visualize sensor data effectively.
Through this project, I developed proficiency in sensor integration, signal conditioning, and the use of National Instruments DAQ systems. I gained valuable insights into the importance of ergonomic design and user-centric solutions in engineering. The Strike Board not only honed my technical skills but also emphasized the need for collaboration, as I worked closely with my team to troubleshoot challenges and refine the system.
This experience deepened my understanding of how engineering principles can be applied to solve practical problems, preparing me to contribute effectively to innovative projects in a professional engineering environment.

Reflection [Strike board]
The Strike Board project was a significant milestone in my journey as an aspiring mechanical engineer, offering lessons and opportunities for growth.
One of the primary challenges I faced during the project was ensuring the accuracy and reliability of the data from the sensors. The resistive force sensors and accelerometers were sensitive to minor variations, introducing noise into the data. Calibrating these sensors to deliver consistent and meaningful outputs required extensive troubleshooting and experimentation. Additionally, integrating the hardware with the LabVIEW software posed technical difficulties, especially in synchronizing real-time data visualization with sensor inputs.
Another challenge was optimizing the ergonomics of the board to ensure ease of use while maintaining functionality. Balancing user comfort with system performance required careful design considerations and iterative testing.
A takeaway from this project was learning how to work effectively within a team. Regular check-ins and clear communication with my teammates were critical in ensuring the project stayed on track. I learned to share updates on my progress, solicit feedback, and coordinate tasks efficiently, which enhanced the project’s outcome and strengthened our collaboration.
Looking back, there are several aspects I would approach differently. First, I would allocate more time for sensor calibration and testing early in the project timeline to mitigate data inaccuracies. Implementing redundancy in the sensor layout or incorporating higher-quality sensors could have further improved reliability. I would also explore advanced filtering techniques for data processing to reduce noise.
This project taught me the technical know-how of sensor integration and data acquisition and emphasized the importance of teamwork, adaptability, and attention to detail in engineering design. It reinforced my enthusiasm for creating practical solutions that address real-world challenges, and I am eager to apply these lessons to future projects as I continue to grow as an engineer.